Read the trends and take unique approaches for a new challenge
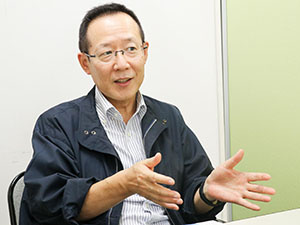
Mr. Yoshikatsu Nishimura, Chief / Vice Director of Osaka Lab
Conclusive fact in introducing TS500P-3200 / Monti Mod.901-3600
- Capability to stably operate 3.2m-wide printing
- Great merit from print speed improvement
From processing station for professional photographers to lab capable of large-size printing
PROTEC is a firm started as a processing station for professional photographers. It was established in 1973. Professional photographers used to use positive films in those days. So our main jobs were development, duplication and print of positive films such as 35mm, 4x5, and Brownie. Later, with the start of the Heisei era, the photography industry accelerated its moves toward digitization.
We also judged that the era of digital camera is coming and the “processing” jobs will decrease. It made us set our direction toward large-size printing.
The machine we first introduced was water-based printer of ENCAD from U.S. I guess it is about 25 years ago. Then we introduced domestic and overseas solvent printers. But solvent machines in those days had strong smell and were not good for health. We also had print heads clogged frequently. That was when we were recommended MIMAKI printers by one of our agents.
The first MIMAKI machine we introduced was “JV3”. It was designed compact with the width of 1.3m and was reasonably priced, which made us feel like giving it a try. But it turned out to be very useful and the maintenance was easy. We realized that nothing is better than domestic machines. As MIMAKI's support system is solid, we renewed our awareness of MIMAKI as a reliable manufacturer from that point too.
Introduction of MIMAKI's machines expands our business
In the days when we started large-size print, many companies used to still use block copies for production. So we sometimes scanned block copies we received, and used them as drafts to create digital data for printing. Thinking about it now, I see it is unbelievable. In other words, that meant we were so early to enter the digital world. We had hardships because of that, but they developed human resources capable of digital works in-house at an early stage, and enabled us to respond to various situations ahead of others.
Also, MIMAKI improves specifications of their printers year after year, which makes us introduce new machines each time.
Once when the back boards for press conference became the rage 5-6 years ago, our JV34-260 did great jobs. As fabric back boards are easy to handle and compact for storage, they are now used commonly not only by companies but also by governments and schools.
It is another advantage of MIMAKI that winding is stable even in wide printing. It winds even long rolls steadily while keeping optimum tension, which makes us rely on the machine to print textiles.
Furthermore, we enjoy unmanned operation for long-time printing. We set the job in the evening, and the print is done in the morning. I think it is contributing to our reform of working practices.
Further low cost and short delivery realized by the newly introducedTS500P
Last year, we succeeded in further improving our operational efficiency by introducing TS500P-3200 and Monti Mod.901-3600 (sublimation transfer press machine).
For instance, when we print a large-sized soft signage, we need the width for sewing the bag-like section to hang the signage from a pole. As we could not keep such a width on top of the data, we used to have to print it separately. This doubled the print time, textiles used, and sewing time and efforts, which made the production very inefficient. We also had to see large parts of textiles go to waste, which raised issues on cost. Capability to print up to 3.2m in width changed the situation. We became able to print a soft signage at one time, including the width for sewing bags added on top of the data. This change allowed us to save time and cost.
We also gained great merit from print speed improvement. The maximum speed of 180m2/h amazed us. With increasingly severe demands for short delivery from customers, we regard it as a machine with the capability to respond to them.
Grasp the needs of customers and develop new original products
Recently, we receive increasing number of orders from drug companies and universities for printing presentation data for academic conference onto textiles instead of panels previously used. While panels need to be sent by package-delivery service because they have a frame, textiles can be folded and carried by the customers themselves.
There are times when we are struck by ideas like this in our daily business. In the days ahead, we hope to grasp the needs of customers without being obsessed with fixed ideas, and make our special and unique proposals.
One of the products we newly introduced this year is decoration tapestry that we call “Deco-Tape”. It is not just a printed tapestry, but is decorated with ribbons or laces. We started to promote it to photo studios and hair salons which have demands for occasions such as Shichi-go-san (event to celebrate children's growth) and coming-of-age ceremony. This idea was generated because we have in-house staff capable of sewing.
This is just an example of the enormous potential of textile that are definitely expanding in the large-size printing field as well. Out of consideration to environment, I anticipate that print on materials that do not generate industrial waste will become the mainstream in the future.
We hope to keep on moving with the new trends, fully operating our MIMAKI machines.
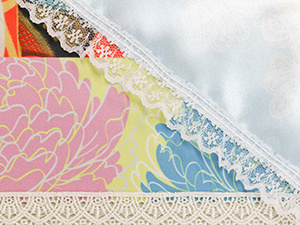
“Deco-Tape” --- Tapestry with a ribbon or other decoration sewn on
PROTEC, Co., Ltd.
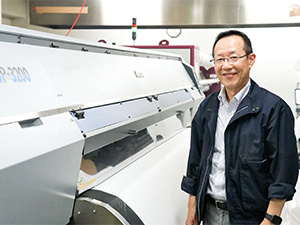
Established in 1973. The company changed its direction from processing station for professional photographers to large-size digital printing ahead of the times.
While handling various kinds of outdoor and indoor signage, it always looks ahead to the future to develop its business such as design of event booth and development of original products.
<Introduced products>
3.2 m Superwide Format Sublimation transfer inkjet printer: TS500P-3200
Sublimation transfer inkjet printer: JV34-260
Sublimation transfer inkjet printer: JV300-160
Sublimation transfer inkjet printer: TS300P-1800
Super-wide roll sublimation transfer press machine: Monti Mod.901-3600
User profile
- NamePROTEC, Co., Ltd.
- IndustryDigital print, outdoor signage (horizontal/vertical banners, flags), production of large display, production of video contents
- Address2-3-20 Minamimorimachi, Kita-ku, Osaka City, Osaka, Japan
- Phone number+81-6-6361-1061
- URLhttp://www.kk-protech.jp